 |

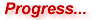
Great things are not done by impulse, but a series of small
things brought together.
- Vincent van Gogh
|

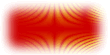

© Copyright 2021
Ribek Technology
All Rights Reserved
|
|
|
These are
some examples of projects from the files at RIBEK. |
|
Project: Nano Particle Dispersions
for Solar Photovoltaic Application
Client: Technology
Start-Up
Objective: Develop
dispersion chemistry and process
Functional nano-particulate materials had been selected for the
application, but there was process technology to successfully deploy
them. RIBEK developed a dispersion vehicle (solvent system and surfactants)
through a series of designed experiments. Prototype coatings were produced
for evaluation. A laboratory-scale bench dispersion process was also
developed using media milling technology. This process technology transfer
enabled the client to produce dispersions on-site and proceed to the
pilot production of functional coatings.
|
Project:
Chemical Sensor Coating
Client: Technology
Start-Up
Objective: Develop
and scale-up ultrasonic coating method.
Build pilot coater and direct the
production of 5000 prototype sensors.
A research firm had developed coated
sensor technology a for detecting airborne
hazardous chemicals. RIBEK entered the project
at the end of the feasibility stage: single
sensors were being produced. The client was
required to deliver a large number of protoype
sensors to their customer for evaluation.
RIBEK refined the ultrasonic coating technique,
designed and built an automated pilot-coater
to produce large numbers of sensors. The
software interface on the automated coater
allowed for rapid training of technicians,
meeting the delivery requirements.
|
Project:
Medical Device Coating
Client: Medical
Device Company
Objective: Dispersion
process development
A manufacturer of point-of-care blood
monitors uses a coated dispersion as the
core of the analytical product. The volume
of the product was expanding beyond the limits
of the current (lab scale) system. Variation
in the product was compensated for by individual
lot analysis. This approach was unacceptable
for the larger production volume. The existing
bench-scale techniques required upgrading
to meet the larger product volume and to
reduce the dependency on lot-by-lot inspection.
Process development was conducted to select
equipment and procedures to satisfy the requirements
for increased production volume and to reduce
lot-to-lot variation.
|
Project:
Nano-Particle Dispersion for Conductive Coating
Client: Contract
Research Firm
Objective: Investigate
conductivity improvement in conductive
polymer
A contract research firm was developing a
novel conductive-polymer coating for aerospace
applications. The conductive polymer alone
exhibited insufficient conductivity to meet
the application requirements. An approach
was developed which attempted to introduce
metallic nano-particles into the coating
to increase the bulk conductivity. RIBEK
was contracted to develop dispersion methods
for the nano-particles. Numerous attempts
were made to produce nano-dispersions. SEM
analysis revealed that the metallic particles
were not in the nano-size range, but were
actually large, highly- fused agglomerates!
The dispersion work was suspended until true
nano-sized metallic particles were available.
|
Project: Ink Dispersion
Process Improvement
Client: Pigment
Manufacturer
Objective: Ink
Dispersion Process Improvement
A pigment manufacturer
had just acquired a pigment
dispersion business as a
strategic expansion of their
operations. The existing
business operated as a specialty,
with high variation in batch
quality. The client intended
to increase the volume of
dispersed pigment, and this
required a scale-up and improvement
of the process. A two-day
on-site consultation was
conducted to review the existing
processes. Equipment configuration,
process strategy, and quality
control measures were developed
to enable the scale-up of
the product line.
|
Project: Equipment Performance
Study
Client: Process
Equipment Manufacturer
Objective: Independant capability
study vs competitor
A manufacturer of process equipment
had acquired a new product line of
horizontal bead mills of unique design.
The performance of the mills had been
anecdotally reported to be superior
to conventional horizontal disk mills,
but definitive data was not available.
A set of designed experiments was conducted
to compare the client's mill with competitor's
equipment. Several products were processed
on both mills, and particle size data
was related to milling parameters such
as energy input and residence time.
A report to the client summarized the
results of the study. This work clearly
showed that the unique design of the
mill produced real advantages for its
users. This report provided unbiased
information that was very useful in
marketing the equipment to potential
customers.
|
|


|
|
 |
 |